Caparo has established a world-class Aluminium foundry to manufacture intricate Aluminium castings through High Pressure Die Casting and Gravity Die Casting processes.
A dedicated workforce of 850 employees, in-depth metallurgical know-how, capabilities in design and engineering, modern technology all come together to make us a preferred partner for our clients.
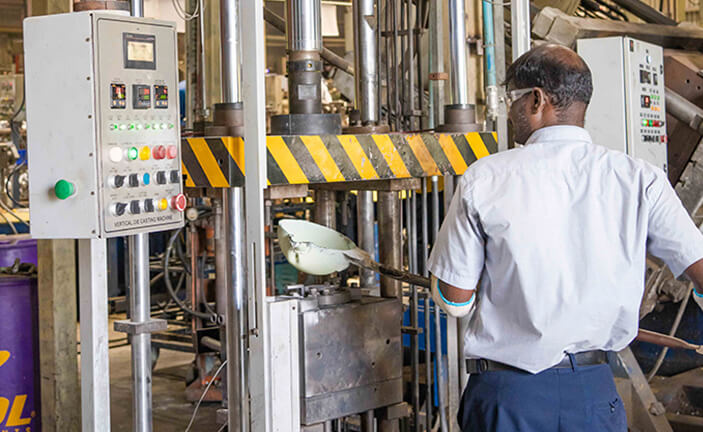
Our design and development department is equipped with latest software and manned by seasoned professionals having a penchant for technology.
Having proven capabilities in 3D Modeling, Rapid Prototyping, Soft Tooling, Permanent Tooling and Reverse Engineering, the design team tirelessly works towards optimizing the existing solutions and developing the new.
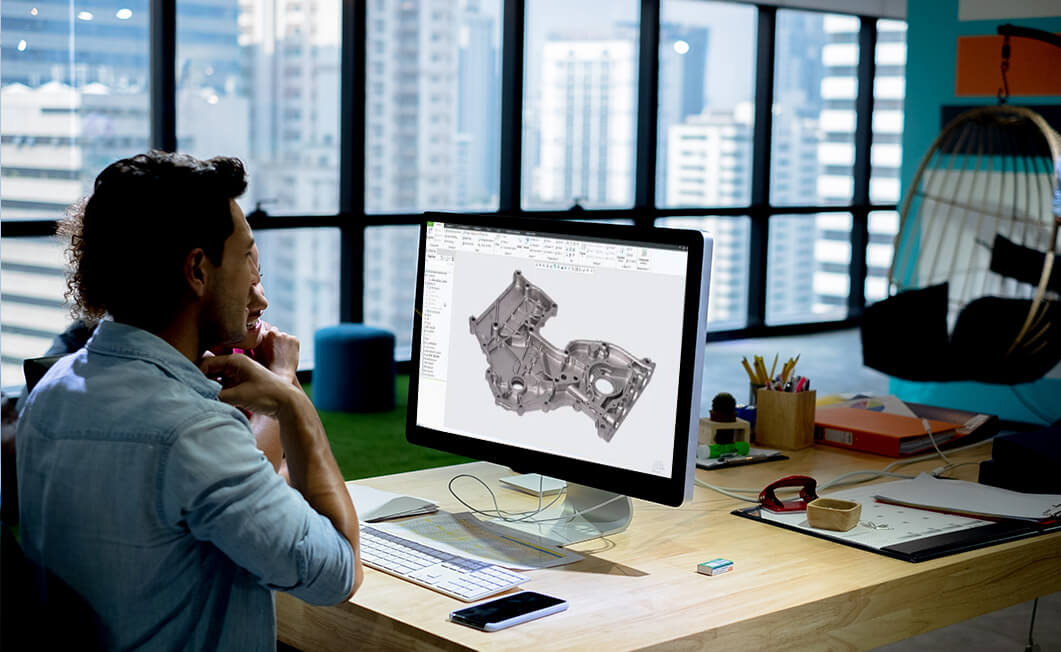
We are committed to achieving excellence and settle for nothing less than the best to provide our customers with high productivity, unmatched quality and timely delivery. To continuously improve on the quality parameters, we follow PDCA (Plan, Do, Check and Act) Cycle for better quality monitoring, effective implementation as well as evaluation of the processes.
